Wässrige Dispersionspolymere wie VAE werden in vielen textilen Prozessen eingesetzt, z. B:
- Tufting
- Herstellung von Vliesstoffen (Bindemittel für Fasern)
- Airlaid
- Wetlaid
- Drylaid
- Nähgarn
- Druck (Primer und Bindemittel für Tinte)
- Fertigstellung
- VAE-Polymere bieten eine hervorragende Haftung an Zellulosefasern
- VAE-Polymere unterstützen die hydrophilen und saugfähigen Eigenschaften stark
- Beschichtungen (z.B. Glasfasergelege für Bedachungen und WDVS)
- Kleben und Laminieren, Zusammenfügen von Materialien.
- Waschen von Kleidungsstücken
Herstellung von Vliesstoffen
Aber sicher! Lassen Sie uns die faszinierende Welt der Vliesstoffe erkunden und die Unterschiede zwischen Airlaid-, Wetlaid- und Drylaid-Techniken verstehen:
- Airlaid-Vliesstoff:
- Definition: Airlaid-Vliesstoff, auch Airlaid-Papier genannt, entsteht, indem Fasern mit Hilfe von Luft dispergiert und anschließend miteinander verklebt werden.
- Prozess:
- Fasermischung: Verschiedene Materialien wie Zellstoff, synthetische Fasern oder Naturfasern werden geöffnet und gemischt.
- Web-Bildung: Mit Hilfe von Luft wird ein Netz aus zufällig angeordneten Fasern erzeugt.
- Bindung: Die Fasern werden miteinander verbunden, um das Gewebe zu bilden.
- Anwendungen:
- Airlaid-Vliesstoffe werden für Hygieneprodukte (z. B. Windeln), medizinische Anwendungen (z. B. OP-Mäntel) und saugfähige Materialien verwendet.
- Nassgelegter Vliesstoff:
- Definition: Nassgelegte Vliesstoffe werden hergestellt, indem die Fasern in Wasser suspendiert und dann auf einem beweglichen Sieb abgelegt werden.
- Prozess:
- Faseraufhängung: Fasern (oft Zellstoff) werden mit Wasser zu einem Brei vermischt.
- Bildschirmablage: Der Schlamm wird auf ein Sieb oder ein Förderband aufgegeben.
- Entwässerung und Verklebung: Das Wasser wird entfernt, und die Fasern werden miteinander verbunden.
- Anwendungen:
- Nassgelegte Gewebe werden häufig für Filtermedien, Wischtücher und Spezialpapiere verwendet.
- Trockengelegter Vliesstoff:
- Definition: Trockengelegter Vliesstoff wird durch Anordnen von Fasern ohne Verwendung von Wasser oder flüssigen Bindemitteln hergestellt.
- Prozess:
- Kardieren: Die Fasern werden von den Ballen gelöst und gemischt. Eine Kardiermaschine kämmt die Fasern zu einem Vlies.
- Bindung: Die Bahn wird mit Methoden wie thermischer Bindung (Hitze und Druck), mechanischer Bindung oder chemischer Bindung verfestigt.
- Arten von Drylaid:
- Kardiert Trockengelegt: Parallel gelegte oder ungeordnete Bahnen mit guter Zugfestigkeit.
- High Loft (Kurzfaser) Drylaid: Erzeugt voluminösere Produkte.
- Anwendungen:
- Trockengelegte Vliesstoffe werden für Bekleidung (z. B. Regenmäntel), Outdoor-Ausrüstung und verschiedene industrielle Anwendungen verwendet.
Jede Technik hat ihre eigenen Eigenschaften, so dass Vliesstoffe vielseitig einsetzbar sind und wahrscheinlich eine angepasste Bindemittelformulierung haben.
Nähgarn
Nähgarn spielen bei der Herstellung von Kleidungsstücken eine entscheidende Rolle und wirken sich sowohl auf die Ästhetik als auch auf die Leistung aus.
- Funktion von Nähfäden:
- Kleidungsstücke zusammenhalten: Nähfäden sind die nur Trimmung der ein Kleidungsstück zusammenhält. Ohne Faden würde das Kleidungsstück einfach auseinanderfallen.
- Bestimmung des Aussehens: Die Wahl des Garns beeinflusst das Aussehen des Kleidungsstücks.
- Beeinflussung der Leistung: Die Fäden beeinflussen die Leistung des Kleidungsstücks während des Tragens und Gebrauchs.
- Faktoren, die die Gewindeauswahl beeinflussen:
- Ästhetik:
- Farbe und Glanz: Berücksichtigen Sie Farbe und Glanz des Garns für dekorative Zwecke wie Absteppungen oder Stickereien.
- Farbton und Farbabstimmung: Achten Sie darauf, dass der Faden zum Stoff passt.
- Farbechtheit: Das Garn sollte auch nach dem Waschen seine Farbe behalten.
- Leistung:
- Die in Kleidungsstücken verwendeten Fäden müssen dauerhaft:
- Nahtstärke: Die Fäden sollten Dehnung, Erholung und Abnutzung standhalten.
- Abnutzungswiderstand: Fäden halten der Reibung beim Nähen und bei der Fertigstellung von Kleidungsstücken stand.
- Elastizität: Die Gewinde müssen sich biegen lassen, ohne zu brechen.
- Chemische Beständigkeit: Die Gewinde sollten gegen Beschädigungen durch Chemikalien beständig sein.
- Entflammbarkeit: Berücksichtigen Sie Sicherheitsaspekte.
- Nähbarkeit:
- Bezieht sich auf die Leistung eines Fadens beim Nähen.
- Zu den Parametern für hervorragende Nähbarkeit gehören:
- Keine Brüche beim Schnellnähen.
- Konsistente Stichbildung.
- Keine übersprungenen Stiche.
- Gleichmäßige Spannung beim Nähen.
- Hohe Abriebfestigkeit.
- Glatte Oberfläche für leichten Durchgang durch Maschinenführungen.
- Die in Kleidungsstücken verwendeten Fäden müssen dauerhaft:
- Ästhetik:
- Gewinde-Klassifizierung:
- Themen können nach folgenden Kriterien klassifiziert werden:
- Substrat:
- Natürliche Fäden: Wird heute kaum noch verwendet, aber Baumwollgarn ist ein Beispiel dafür.
- Synthetische Fäden: Bevorzugt wegen der hohen Zähigkeit, Abriebfestigkeit und chemischen Beständigkeit.
- Konstruktion:
- Fäden können unterschiedliche Konstruktionen haben (z. B. gesponnen, fadenförmig, kerngesponnen).
- Oberfläche:
- Gewinde können Oberflächenbehandlungen wie Schmierung oder Verklebung aufweisen.
- Substrat:
- Themen können nach folgenden Kriterien klassifiziert werden:
Die Auswahl des richtigen Nähfadens ist entscheidend für eine gute Nähleistung und die gewünschte Nahtqualität. Die Verwendung der falschen Art oder Größe kann zu Fehlern und längeren Durchlaufzeiten führen. Diese können durch den Zusatz einer der VAE-Beschichtungen von Intercol weiter verbessert werden.
Textildruck
Polymere spielen eine entscheidende Rolle beim Textildruckdie sowohl die Ästhetik als auch die Funktionalität verbessern.
- Pigmentdruck-Bindemittel:
- Definition: Pigmentdruckbindemittel sind filmbildende Materialien, die aus langkettigen Makromolekülen bestehen.
- Funktion: In Verbindung mit Pigmenten bilden diese Bindemittel ein dreidimensionales Netz auf dem Stoff.
- Anmeldung: Sie werden häufig verwendet in Textil-Pigmentdruck zur Fixierung von Pigmenten auf der Stoffoberfläche, um Farbechtheit und Haltbarkeit zu gewährleisten.
- Additive Fertigung (3D-Druck) auf Textilien:
- Übersicht: Die additive Fertigung (AM), auch bekannt als 3D-Druck, hat sich über das Prototyping hinaus zu einer fortschrittlichen Fertigung entwickelt.
- Vorteile von AM in Textilien:
- Geometrische Flexibilität: Ermöglicht die Optimierung der Produkteigenschaften.
- Änderung der Mikrostruktur und der Eigenschaften: Erreicht durch Metamaterialien.
- Ressourceneffizienz: Verbraucht weniger Rohmaterial.
- Cloud-Herstellung: Verkürzung der Lieferketten und Förderung der Nachhaltigkeit.
- Herausforderungen: Trotz der Fortschritte bei der Anwendung von AM auf Textilien gibt es Probleme mit der Skalierbarkeit und die Forschung befindet sich noch in einem frühen Stadium.
- Anwendungen:
- Funktionale Filamentfasern/Drähte: Entwicklung von Funktionsfasern für textile Flächengebilde.
- 3D-Druck auf Textilien: Erstellen komplizierter Muster und Strukturen.
- 3D-Druck fertiger Kleidungsstücke: Anpassbare und nachhaltige Produktion.
- 4D Textilien: Materialien, die im Laufe der Zeit ihre Form verändern.
- Materialien in 3D-gedruckten Stoffen:
- Derzeitige Beschränkungen:
- Steifheit und starre Kleidung: Viele 3D-gedruckte Stoffe führen zu unbequemen Kleidungsstücken.
- Polymere auf Erdölbasis: Die üblicherweise verwendeten Materialien (z. B. ABS, PLA, PU) werden aus Erdöl gewonnen.
- Entdeckung natürlicher Textilfasern: Es wird an der Entwicklung von 3D-Druckmaterialien aus Naturfasern wie Wolle geforscht.
- Derzeitige Beschränkungen:
Zusammenfassend lässt sich sagen, dass Polymere zur Innovation und Nachhaltigkeit des Textildrucks beitragen, sei es durch Bindemittel, 3D-Druck oder die Erforschung neuer Materialien.
Textilveredelung
Textilveredelung bezieht sich auf die Prozesse, die gewebte oder gewirkte Stoffe in ein brauchbares Material verwandeln. Insbesondere umfasst er alle Schritte, die nach dem Färben des Garns oder des Stoffes durchgeführt werden, um das Aussehen, die Leistung oder die taktile Qualität (oft als "Hand" bezeichnet) des fertigen Textils oder der Kleidung zu verbessern.
Beispiele für die Textilveredelung:
- Grauer Stoff: Wenn der Stoff den Webstuhl oder die Strickmaschine verlässt, ist er nicht sofort verwendbar. In diesem Stadium wird es als graues Tuch und enthält sowohl natürliche als auch zugesetzte Verunreinigungen.
- Zweck der Veredelung:
- Wertschöpfung: Die Veredelung wertet das Produkt auf und macht es für den Endverbraucher attraktiver, nützlicher und funktioneller.
- Oberflächengefühl und Ästhetik: Techniken wie Bleichen und Färben können auf das Garn vor dem Weben angewendet werden, während andere direkt auf den grauen Stoff nach dem Weben oder Stricken angewendet werden.
- Fortgeschrittene chemische Veredelungen: Beispiele hierfür sind die Verbesserung der Oberflächenbeschaffenheit und die Zugabe fortschrittlicher chemischer Behandlungen.
- Arten von Veredelungstechniken:
- Nassverarbeitung: Dazu gehören Verfahren wie Waschen, Färben und Bleichen.
- Chemische Behandlungen: Es werden verschiedene chemische Behandlungen durchgeführt, um die gewünschten Eigenschaften zu erzielen, wie z. B. Flammschutz, Wasserabweisung und antistatische Eigenschaften.
- Wärmeeinstellung: Synthetische Fasern benötigen oft nur eine Thermofixierung, da sie bereits pflegeleichte Kriterien aufweisen.
- Historischer Kontext:
- Einige Veredelungstechniken, wie das Walken, wurden mit der industriellen Revolution überflüssig.
- Andere, wie z. B. die Merzerisierung, entstanden im Zuge der industriellen Revolution.
Die Textilveredelung spielt eine entscheidende Rolle bei der Verbesserung der Gewebeeigenschaften, der Gewährleistung des Komforts und der Erfüllung der Erwartungen der Verbraucher. VAE-Polymere werden häufig als Bindemittel und Beschichtung verwendet. VAE unterstützen die Flammhemmung, sind mit vielen Additiven kompatibel und sind echte LOW VOC-Bindemittel auf Wasserbasis. VAE eignen sich auch sehr gut für Recyclingzwecke, da sie waschbar und waschbeständig sind, aber auch thermoplastisch sind.
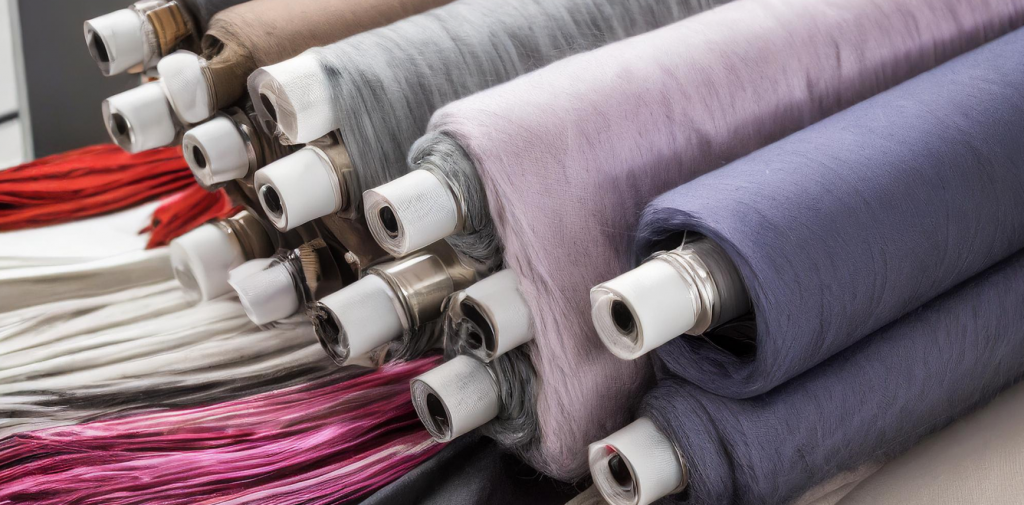
Textilbeschichtungen
Textile Beschichtungen spielen eine entscheidende Rolle bei der Veränderung der Ästhetik und der Funktionalität von Textiloberflächen. Diese Beschichtungen werden auf Textilsubstrate aufgebracht, um deren Eigenschaften zu verbessern und sie für verschiedene Anwendungen geeignet zu machen. Kommen wir nun zu den Einzelheiten:
- Zweck und Bedeutung:
- Ästhetische Aufwertung: Textilbeschichtungen verbessern das Aussehen und die Haptik von Stoffen und führen zu hochwertigen Textilien.
- Funktionsweise: Beschichtungen verlängern die Nutzungsdauer von Textilien, bewahren ihre Ästhetik und bieten Leistungs- und Schutzmerkmale.
- Formulierung und Anwendung:
- Inhaltsstoffe: Eine typische Formulierung einer Textilbeschichtung umfasst polymere Bindemittel zusammen mit Zusatzstoffen wie Farbstoffen, Haftvermittlern, Bioziden und Weichmachern.
- Anwendungstechniken: Beschichtungen werden mit folgenden Methoden aufgebracht Sprühen, Polsterungoder Technologien im Nanobereich.
- Funktionelle Eigenschaften: Beschichtete Textilien können Eigenschaften aufweisen wie wasserabweisende Wirkung, Schwerentflammbarkeitund selbstreinigend.
- Anwendungen:
- Beschichtungen für Bekleidung: Verbesserung der Haltbarkeit, Atmungsaktivität und Ästhetik von Kleidung.
- Beschichtungen für Heimtextilien: Verbesserung der Leistungsfähigkeit von Stoffen für Polstermöbel, Vorhänge und Bettwaren.
- Transport Textilbeschichtungen: Wird in der Innenausstattung von Kraftfahrzeugen, Flugzeugen und im Schiffsbau verwendet.
- Technische Textilbeschichtungen: Für geotechnische, medizinische und industrielle Textilien.
- Innovationen und zukünftige Trends:
- Fortgeschrittene Techniken: Die digitale Beschichtungstechnologie und die Sol-Gel-Chemie bieten spannende Möglichkeiten.
- Multifunktionale Textilien: Die Nachfrage nach Textilien mit mehreren Funktionen nimmt zu.
Textilbeschichtungen schließen die Lücke zwischen Ästhetik und Zweckmäßigkeit und tragen zu einem breiten Spektrum von Anwendungen in verschiedenen Branchen bei.
Insbesondere VAE-Polymere unterstützen die Verwendung von Additiven, da sie häufig nichtionisch sind, einen niedrigen Entflammbarkeitsindex aufweisen und (in Wasser/Lösungsmittel) löslich (z. B. für Recyclingzwecke) oder vernetzbar und waschbar sein können.
Kaschieren von Textilien
Laminiertes Gewebe ist eine faszinierende Verschmelzung von traditionellen Textilien und moderner Technologie und wird in verschiedenen Branchen eingesetzt:
- Laminiertes Gewebe:
- Laminiertes Gewebe ist im Wesentlichen eine Kombination aus mehreren Lagen verschiedener Materialien, die miteinander verbunden werden, um eine einzige Lage mit verbesserten Eigenschaften zu schaffen.
- Die Schichten umfassen in der Regel:
- Textile Basisschicht: Diese Schicht sorgt für die Struktur des Gewebes und bestimmt oft seine Textur und sein Aussehen. Zu den gängigen Grundgeweben gehören Nylon, Polyester und verschiedene Mischgewebe.
- Wasserdichte oder wasserabweisende Schicht: Diese Schicht wird auf die Basisschicht aufgetragen und schützt vor Feuchtigkeit. Sie besteht oft aus Polyurethan oder einem anderen wasserdichten Material. Speziell behandelte Versionen sind wasserabweisend und widerstehen dem Eindringen von Flüssigkeiten.
- Zusätzliche Verstärkungsschichten (manchmal): Diese Schichten erhöhen die Haltbarkeit und Festigkeit.
- Der Klebeprozess kann durch Methoden wie Hitze und Druck, Klebstoffe oder fortschrittliche Techniken wie Ultraschallschweißen erreicht werden.
- Anwendungen von Laminatgeweben:
- Outdoor-Ausrüstung:
- Laminierte Stoffe haben die Outdoor-Branche revolutioniert.
- Beispiele sind Regenjacken, Skihosen, Zelte, Rucksäcke und Handschuhe.
- Die wasserdichte Schicht hält die Feuchtigkeit ab, während die untere Textilschicht für Haltbarkeit und Komfort sorgt.
- Medizinische und Hygieneprodukte:
- Unverzichtbar in den Bereichen Medizin und Hygiene.
- Wird in OP-Kitteln, Abdeckungen und medizinischer Einwegkleidung verwendet.
- Die wasserdichte Schicht sorgt für eine sterile Umgebung.
- Wird auch in Windeln und anderen Hygieneprodukten verwendet, um Weichheit, Komfort und Flüssigkeitsbeständigkeit zu gewährleisten.
- Mode und Bekleidung:
- Modedesigner schätzen den laminierten Stoff wegen seiner einzigartigen Eigenschaften.
- Ermöglicht die Herstellung modischer, wetterfester Kleidungsstücke.
- CPSIA-konform, erfüllt Kindersicherheitsstandards.
- Sie werden für Regenmäntel, Ponchos und sogar für Schuhe verwendet, die an regnerischen Tagen die Füße trocken halten.
- Outdoor-Ausrüstung: